Mastering the Art of Injection Mold Plastics for Innovative Business Solutions
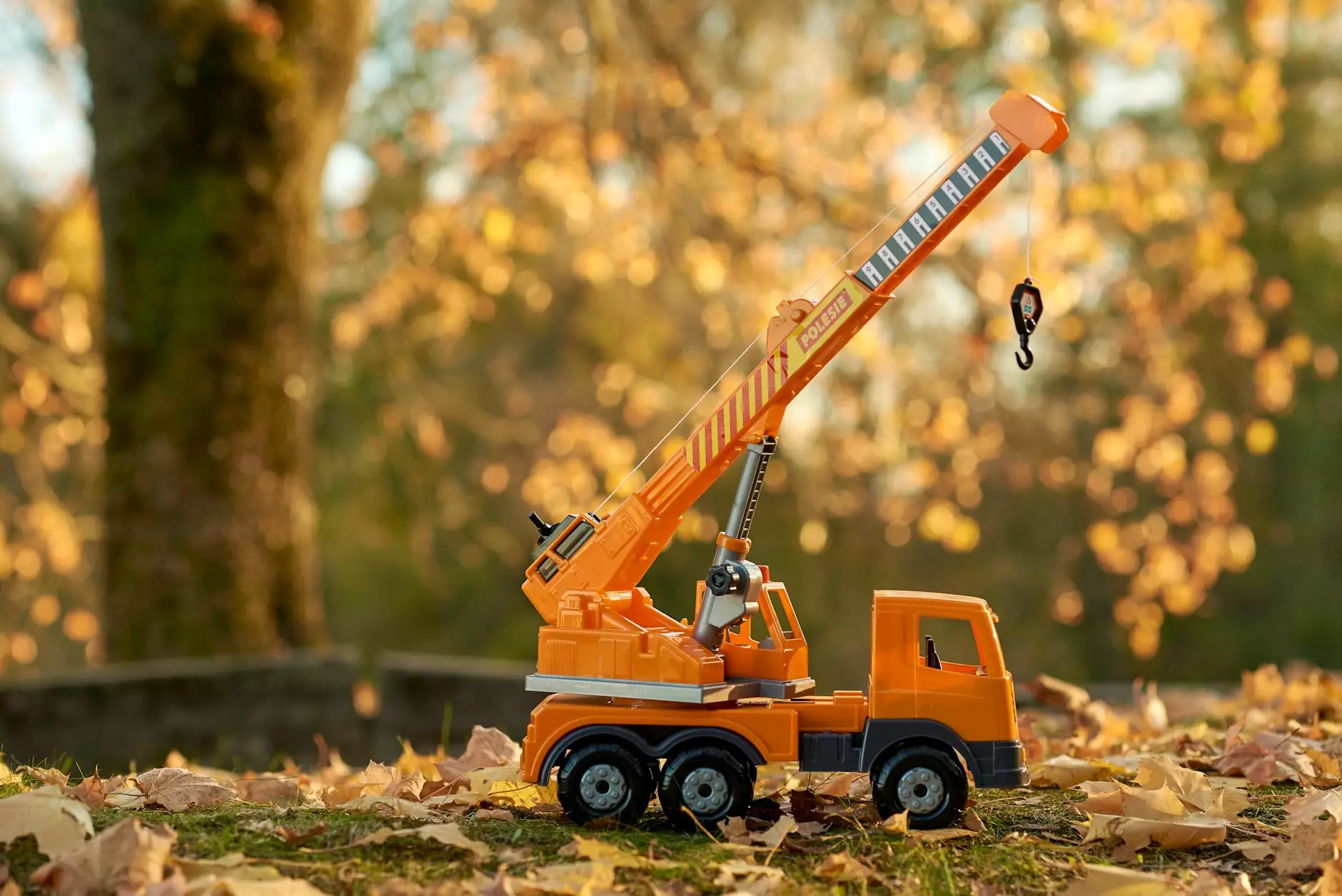
In the ever-evolving world of manufacturing, staying ahead of the curve is crucial. One of the most significant advancements in this field is the use of injection mold plastics. This method has not only transformed the quality and efficiency of production but also opened up new avenues for innovation and sustainability. In this comprehensive guide, we will delve into the intricacies of injection mold plastics, their benefits, applications, and how they fit into the broader landscape of business, particularly for metal fabricators.
Understanding Injection Mold Plastics
Injection molding is a manufacturing process where molten materials, typically plastics, are injected into a mold. This technique allows for the production of complex shapes and high precision parts at a rapid pace. The materials used in this process are crucial, and that's where injection mold plastics come into play.
What Are Injection Mold Plastics?
Injection mold plastics are specially formulated polymers that are engineered to withstand the demands of the injection molding process. They are characterized by their ability to be melted, injected into molds, and then cooled into solidified forms. Common types include:
- Polypropylene (PP) - Known for its good chemical resistance and flexibility.
- Polyethylene (PE) - Durable and lightweight, ideal for various applications.
- Polystyrene (PS) - Generally used for low-strength applications, easy to mold.
- Polyvinyl Chloride (PVC) - Highly versatile and used in construction and medical applications.
- ABS (Acrylonitrile Butadiene Styrene) - Known for its impact resistance and toughness.
The Role of Injection Mold Plastics in Metal Fabrication
For metal fabricators, the integration of injection mold plastics represents a paradigm shift. Traditionally, metal fabrication involved processes such as cutting, welding, and machining. However, the combination of metals with injection mold plastics enables the creation of lightweight yet robust components.
Benefits of Using Injection Mold Plastics in Metal Fabrication
Integrating injection mold plastics into metal fabrication offers numerous advantages:
- Weight Reduction: Components made from plastics are significantly lighter than those made entirely of metal, improving efficiency in various applications.
- Cost-Effectiveness: Molding plastics can reduce overall manufacturing costs, minimizing material waste and labor expenses.
- Design Flexibility: Injection molding allows for complex geometries that would be difficult or impossible to achieve with traditional metalworking techniques.
- Enhanced Performance: Certain plastics can offer superior resistance to corrosive environments, extending the lifespan of components.
- Sustainability: Many injection mold plastics are recyclable, aligning with the growing demand for environmentally friendly production practices.
Applications of Injection Mold Plastics Across Industries
The versatility of injection mold plastics means they find applications across a wide array of industries:
Automotive Industry
In the automotive sector, manufacturers utilize injection mold plastics for:
- Interior Components: Dashboard panels, door handles, and trim parts that require both aesthetic appeal and durability.
- Engine Components: Lightweight plastic parts that can withstand heat, reducing overall vehicle weight.
- Exterior Body Parts: Making bumpers and fenders that are both strong and flexible.
Consumer Electronics
In consumer electronics, injection mold plastics are pivotal in the production of:
- Casings: Providing a protective and appealing exterior for devices.
- Connectors and Components: Essential components that require precision and durability.
Medical Applications
In the medical field, the reliability of injection mold plastics is crucial. They are utilized in:
- Disposable Medical Supplies: Syringes, vials, and other equipment that require sterile, single-use plastic.
- Medical Device Housings: Providing protective barriers for sensitive electronic components.
Consumer Products
From household items to sporting goods, injection mold plastics are used in:
- Kitchenware: Utensils, containers, and other durable goods.
- Toys: Safe, colorful, and lightweight materials that promote creativity and fun.
Innovations in Injection Mold Plastics
Continuous research and development in the field of injection mold plastics lead to innovative materials and techniques. Recent trends include:
Biodegradable Plastics
As environmental concerns grow, the development of biodegradable injection mold plastics is gaining traction. These materials can break down naturally, reducing their environmental footprint.
Smart Plastics
Smart plastics are being developed with embedded sensors for various applications. These materials can monitor conditions and even adapt their functions, paving the way for intelligent solutions across industries.
Challenges in Injection Molding
Despite the numerous advantages, there are challenges in the injection molding process, particularly concerning injection mold plastics:
- Material Selection: Choosing the right plastic for specific applications is crucial and requires in-depth knowledge.
- Mold Design: Creating a mold that can withstand high pressure and temperature while maintaining high precision is complex and costly.
- Production Efficiency: Maintaining consistent quality throughout the production run is essential for competitiveness.
Best Practices for Metal Fabricators Utilizing Injection Mold Plastics
For metal fabricators looking to integrate injection mold plastics into their offerings, several best practices can enhance the process:
Invest in Quality Control
Implementing rigorous quality control measures will ensure the durability and reliability of the finished products. This includes testing materials before production and maintaining consistent molding conditions.
Stay Informed on Material Innovations
Keep abreast of the latest advancements in injection mold plastics. This could involve attending industry seminars, subscribing to relevant publications, and engaging with material suppliers.
Design for Manufacturability
When designing new products, consider how the design will impact the injection molding process. This involves understanding the properties of the plastics being used and how they will behave during molding and cooling.
Conclusion: The Future of Injection Mold Plastics in Business
As we reflect on the transformative impact of injection mold plastics, it is clear that they play a vital role in modern manufacturing, particularly for metal fabricators. The ability to produce strong, lightweight, and cost-effective components is essential for staying competitive in today’s market.
By embracing innovations and overcoming the challenges associated with injection molding, businesses can position themselves as industry leaders. The integration of injection mold plastics not only enhances product quality but also contributes to sustainable practices that are increasingly demanded by consumers.
For businesses looking to harness the potential of injection mold plastics, the time to act is now. The future is bright for those who innovate and adapt to the ever-changing landscape of manufacturing. For more insights and tailored solutions in injection molding, visit deepmould.net.