Understanding Hydraulic Ball Valves: A Comprehensive Guide
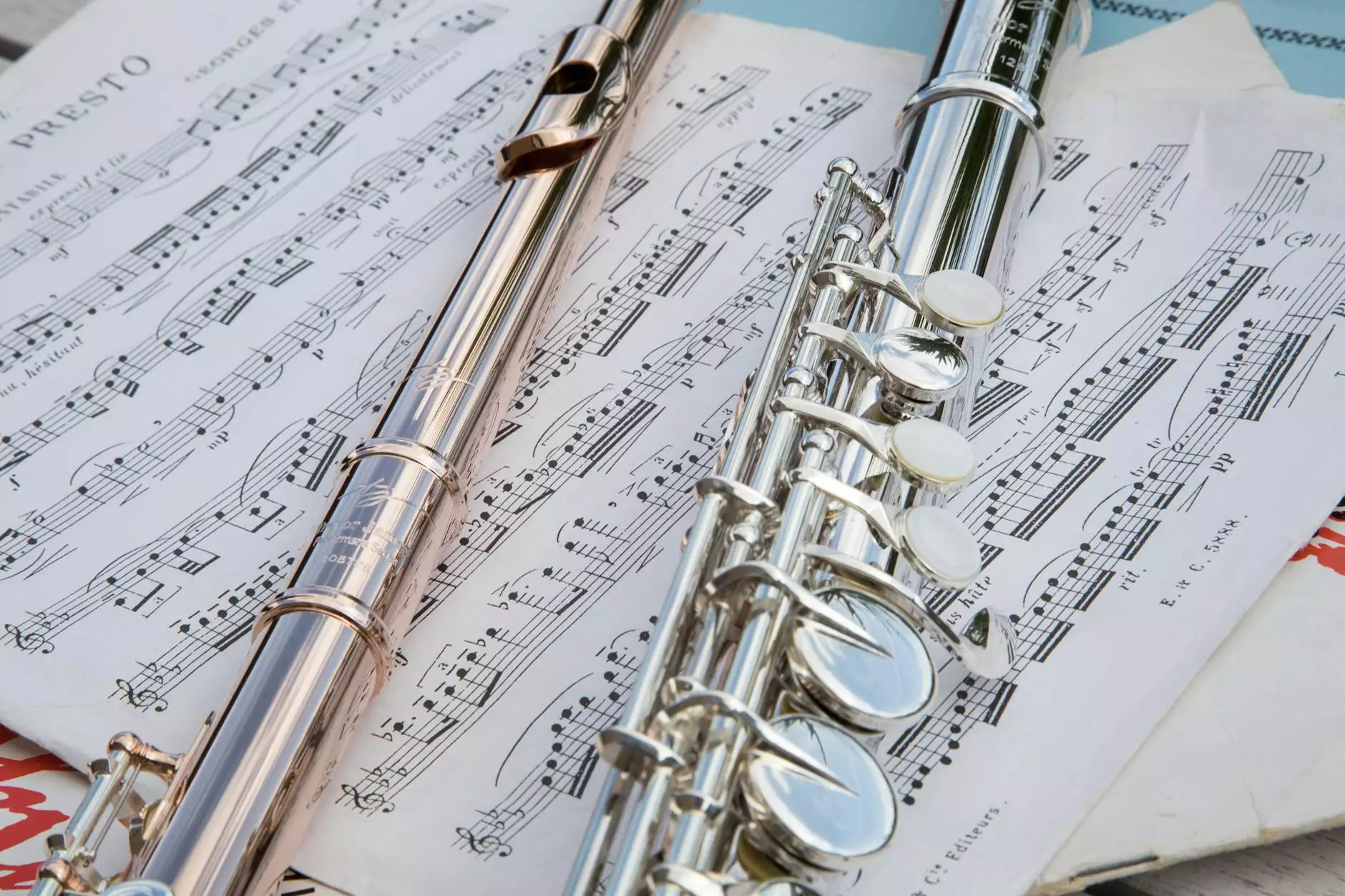
In today’s industrial landscape, the hydraulic ball valve plays a crucial role in fluid control systems. Designed to provide reliable and efficient flow management, these valves are essential in numerous applications, from automotive to manufacturing industries. This article dives deep into the functionality, applications, and benefits of hydraulic ball valves, aiming to equip you with knowledge that can potentially enhance your business and engineering projects.
What is a Hydraulic Ball Valve?
A hydraulic ball valve is a shut-off valve that controls the flow of fluid through piping systems. It operates using a spherical disc, referred to as the ball, which has a hole or port through its center. When the ball is rotated, the hole aligns with the flow path, allowing fluid to pass through. Conversely, rotating the ball 90 degrees blocks the flow. This simple yet effective mechanism allows for both quick shut-off and seamless operation in a variety of conditions.
How Do Hydraulic Ball Valves Work?
The operation of a hydraulic ball valve is both straightforward and efficient:
- Open Position: When the valve is open, the hole in the ball aligns with the fluid path, creating a straight-through channel for fluid to flow.
- Close Position: When the valve is turned to the closed position, the solid part of the ball blocks the flow, completely stopping the passage of fluid.
- Control Mechanism: Hydraulic ball valves can be operated manually via a lever or automatically through various actuation methods such as pneumatic or electric actuators.
Key Components of a Hydraulic Ball Valve
To fully understand hydraulic ball valves, it's essential to familiarize yourself with their key components:
- Body: The main part of the valve that holds all components together.
- Ball: The spherical component that opens and closes the flow path.
- Seats: Sealing components that allow the ball to create a tight seal in either the open or closed position.
- Stem: Connects the ball to the actuator or lever, enabling rotation of the ball.
- Actuator: The mechanism (manual or automated) used to control the valve's position.
Applications of Hydraulic Ball Valves
Hydraulic ball valves have a wide range of applications across different industries, reflecting their versatility and efficiency:
1. Oil and Gas Industry
In the oil and gas sector, hydraulic ball valves are essential for handling high pressures and controlling the flow of crude oil and natural gas. Their reliability ensures minimal leaks and maximum safety in pipeline operations.
2. Water Supply and Treatment
Water treatment facilities utilize hydraulic ball valves for regulating the supply of water, ensuring that systems remain efficient and can handle the variations in pressure that often occur.
3. Chemical Processing
In chemical plants, hydraulic ball valves are employed in the transportation and mixing of various chemicals. Their ability to provide tight seals is vital in preventing contamination and chemical spills.
4. Power Generation
Hydraulic ball valves are critical in the power generation sector, especially in hydroelectric plants and other facilities that require precise flow control to maintain operational efficiency.
5. Automotive Applications
In the automotive industry, hydraulic ball valves aid in various systems, including hydraulics for braking and steering mechanisms, ensuring smoother and safer operation of vehicles.
Benefits of Using Hydraulic Ball Valves
The use of hydraulic ball valves comes with a multitude of advantages:
- Durability: Built to withstand harsh conditions and high pressure, hydraulic ball valves are constructed from robust materials that ensure longevity.
- Low Torque Requirements: They require less force to operate compared to other valve types, making them user-friendly and efficient.
- Quick Operation: The 90-degree turn operation allows for rapid on/off control, improving workflow in fast-paced environments.
- Minimal Leakage: With their sealing mechanism, hydraulic ball valves minimize the risk of leaks, enhancing safety and environmental protection.
- Versatile Design: Available in various sizes and materials, they can be customized for specific applications catered to unique industrial needs.
Choosing the Right Hydraulic Ball Valve for Your Needs
Selecting the appropriate hydraulic ball valve is essential for optimal system performance. Here are key factors to consider:
1. Operating Pressure and Temperature
Ensure that the valve materials can withstand the maximum pressure and temperature of your application. Refer to manufacturer specifications to match the valve’s capability with operational requirements.
2. Material Compatibility
Choose materials that are compatible with the media being transferred. Common materials include stainless steel, brass, and plastic, each offering varying degrees of resistance to corrosion and wear.
3. Size and Flow Requirements
Select a valve size that aligns with the diameter of the piping and the desired flow rate. An oversized valve can lead to energy loss, while an undersized valve can create bottlenecks in fluid movement.
4. Type of Actuation
Determine whether manual or automated actuation works best for your system. Automatic valves often reduce the need for human intervention and improve efficiency.
Installation and Maintenance of Hydraulic Ball Valves
Proper installation and regular maintenance are crucial in ensuring the longevity and reliability of hydraulic ball valves:
Installation:
- Ensure proper alignment: The valve must be installed in a manner that aligns with the flow direction indicated on the valve body.
- Use appropriate sealing techniques: Gaskets and seals must be compatible with the fluids traversing the valve to avoid leakage.
- Check for proper torque: Follow manufacturer guidelines for tightening bolts to avoid damaging the valve body.
Maintenance:
Regular checks and maintenance procedures can greatly enhance the durability and performance of hydraulic ball valves:
- Periodic inspections: Look for signs of wear and tear, especially around the ball and seats.
- Clean components: Regularly remove any debris that may obstruct the valve’s operation.
- Test functionality: Check the valve's operation regularly to ensure it opens and closes smoothly without leaks.
Conclusion: The Essential Role of Hydraulic Ball Valves in Modern Industry
In conclusion, the hydraulic ball valve is a vital component in a multitude of industrial applications, offering reliability, efficiency, and safety. Whether in oil and gas, water treatment, chemical processing, or automotive systems, these valves are engineered to meet the demanding requirements of fluid control. By understanding their functions, applications, and maintenance needs, businesses can make informed decisions that enhance operational efficiency and longevity. For any fittings and valves you require, visit fitsch.cn to explore our wide range of products.